- 2025
-
-
-
-
-
-
-
-
-
-
-
-
-
-
-
-
-
-
-
-
-
-
-
-
- 2010
-
-
-
-
-
-
-
-
-
-
-
-
- 2000
-
-
-
-
-
-
-
-
-
-
-
-
-
-
-
-
-
-
-
-
- 1990
-
-
-
-
-
-
-
-
-
-
-
-
-
-
-
-
-
-
-
-
-
-
-
- 1980
Bally Technologies
Lottery Terminal
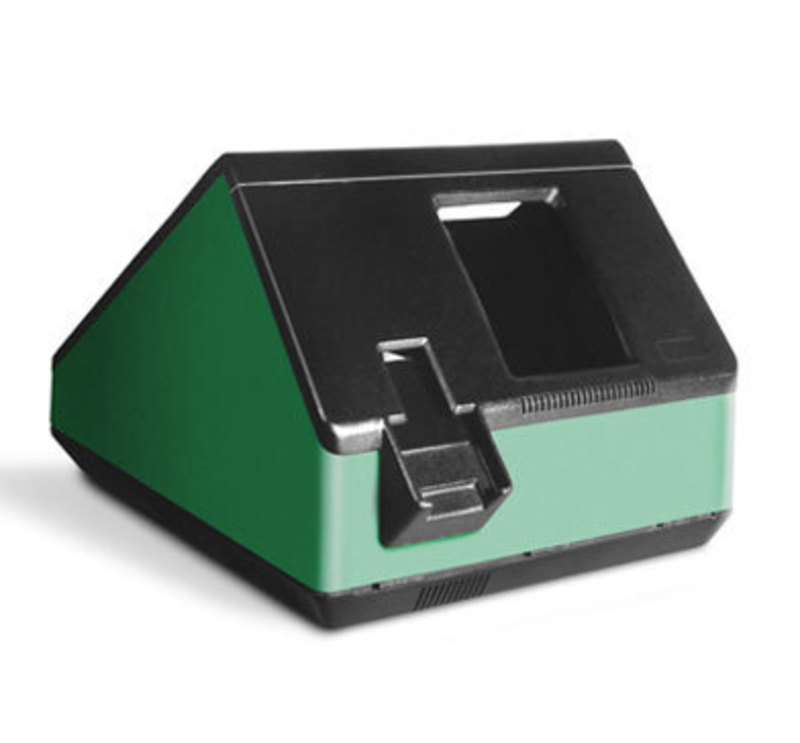
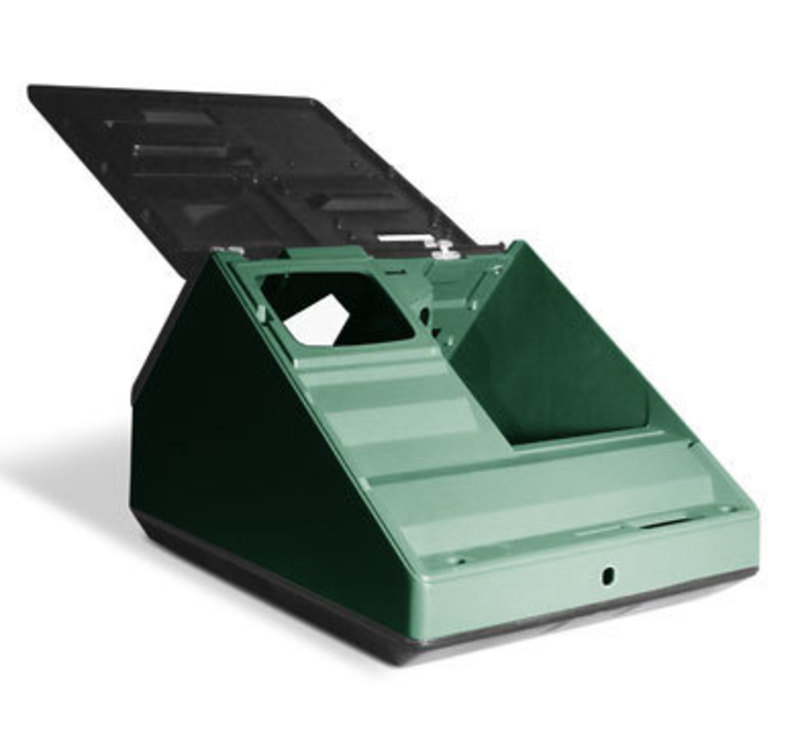
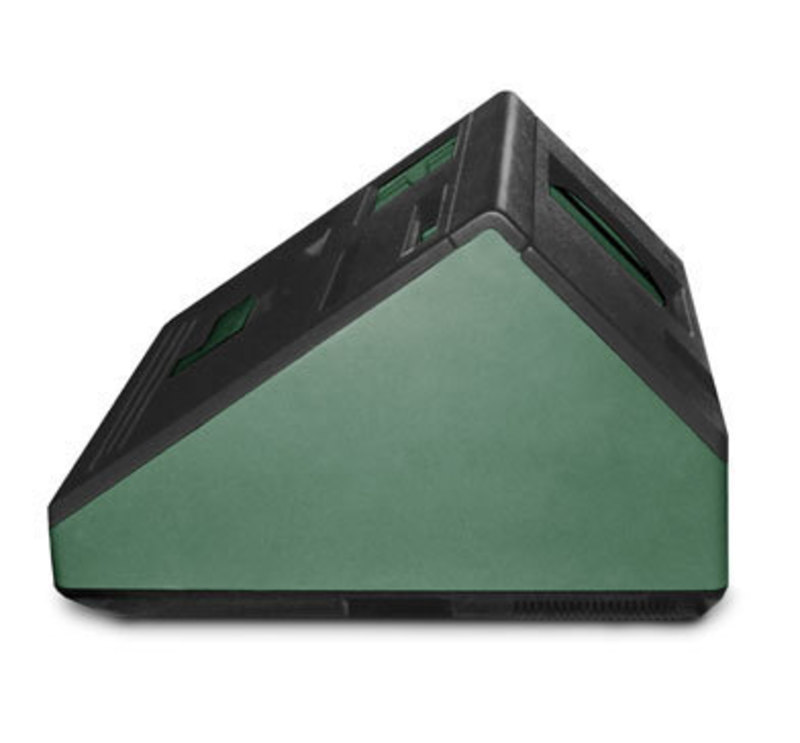
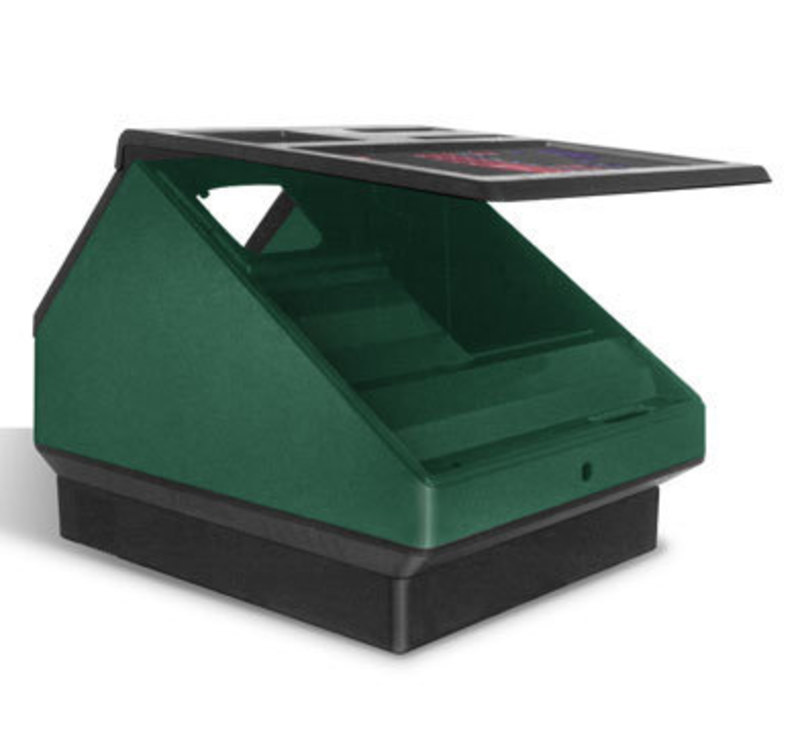
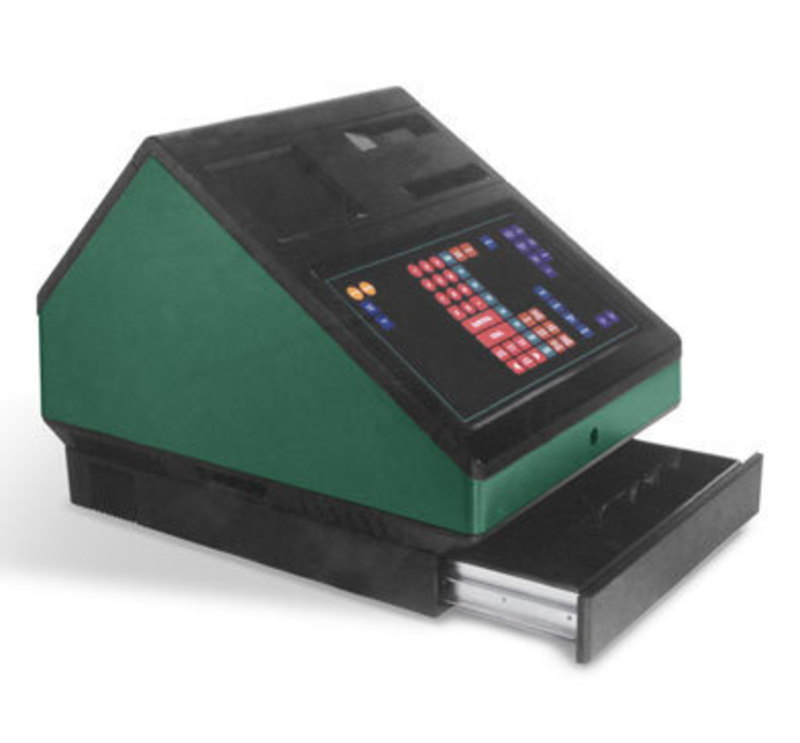
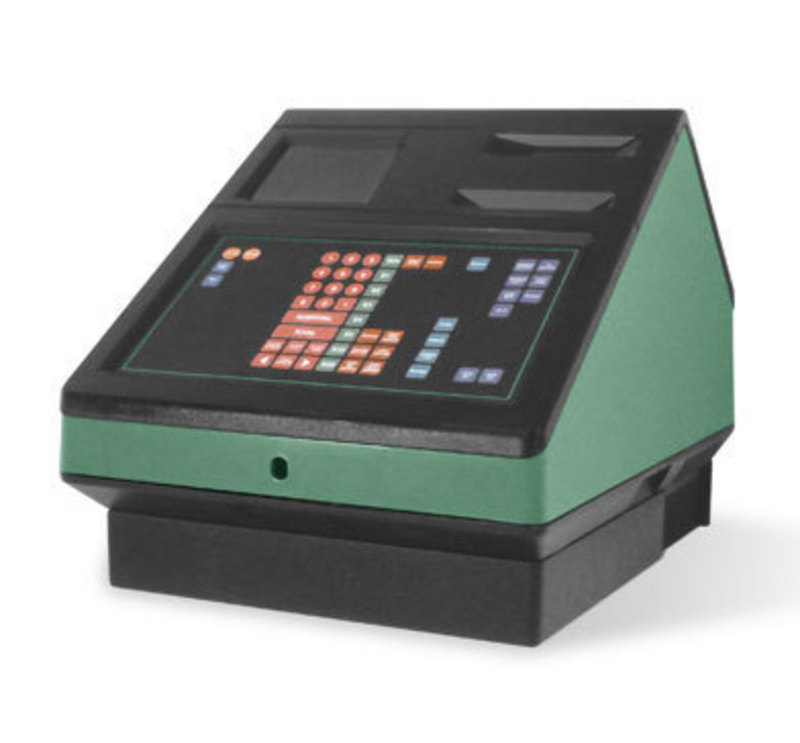
Design Team: Cesaroni Design & Bally Technologies
Bally Technologies worked with Cesaroni Design to develop a new product utilizing structural foam. Working closely with Bally, we executed the structural foam project from sketches, renderings, assembly details, piece part drawings and prototypes.
After analyzing manufacturing processes, a structural foam product emerged as the only logical choice. The use of structural foam assisted in making a product superior in appearance as well as in strength and durability.
Concept renderings were generated to determine the aesthetics. A foam core mockup was then created to quickly test basic ergonomics. A wooden styling model came next, followed by a functional prototype. As each of the 3D form factors was created, more accurate detail drawings were completed.
The structural foam made it possible to keep the size to a minimum. This was partially the result of fewer ribs and support walls needed, which increased internal space for components. The structural foam allowed a minimum of exterior draft on two tall walls. This was a key factor in the overall appearance. To bring the finish of the parts closer to perfection, a smooth fog coat of paint was applied.
Project deadlines were met by keeping lines of communication open between the client, designers, molder and toolmaker.
Bally Technologies
Lottery Terminal
Design Team: Cesaroni Design & Bally Technologies
Bally Technologies worked with Cesaroni Design to develop a new product utilizing structural foam. Working closely with Bally, we executed the structural foam project from sketches, renderings, assembly details, piece part drawings and prototypes.
After analyzing manufacturing processes, a structural foam product emerged as the only logical choice. The use of structural foam assisted in making a product superior in appearance as well as in strength and durability.
Concept renderings were generated to determine the aesthetics. A foam core mockup was then created to quickly test basic ergonomics. A wooden styling model came next, followed by a functional prototype. As each of the 3D form factors was created, more accurate detail drawings were completed.
The structural foam made it possible to keep the size to a minimum. This was partially the result of fewer ribs and support walls needed, which increased internal space for components. The structural foam allowed a minimum of exterior draft on two tall walls. This was a key factor in the overall appearance. To bring the finish of the parts closer to perfection, a smooth fog coat of paint was applied.
Project deadlines were met by keeping lines of communication open between the client, designers, molder and toolmaker.